简单的物理学原理是,车辆越轻,行驶所需的能量就越少;即使汽车重量减轻100公斤, 20万公里的燃油成本也能节省1040美元。这意味着更少的汽油、更少的金钱,以及更少的碳排放。
然而,汽车制造商需要在不牺牲强度和耐用性的前提下减轻车身重量。这就带来了*个问题。如果轻质材料容易变形或耐热性不如重质材料,那么焊接和连接就会更加困难。换句话说,制造轻量化汽车并非仅仅更换金属那么简单。
让我们来探讨*下当今的汽车制造商如何创新金属板连接以及这对未来意味着什么。
汽车工程师在连接金属板时面临的挑战
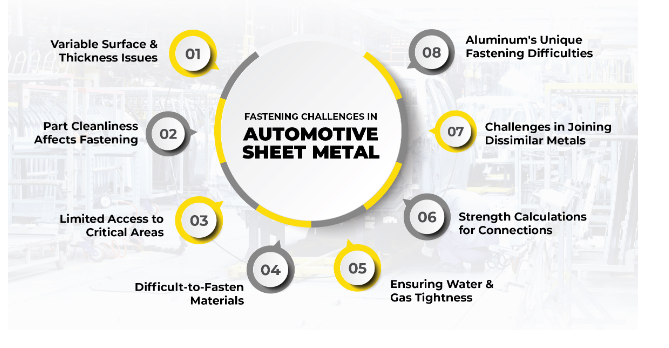
可变的表面条件和厚度
随着铝在车身中的使用日益增多,轻量化汽车制造需要解决这种金属的诸多特性。例如,对于铸件而言,零件的厚度会因观察角度的不同而变化。如果打开这种复杂零件的横截面,就会发现其中存在着不*致性,这会使高质量连接更加困难。而且,这也会使得了解接头参数变得更加困难。
零件清洁度
脏污的金属无法正确焊接在*起。良好、清洁的部件至关重要:污垢、铁锈或油脂等污染物会导致接头强度低和粘附。如果焊缝清洁度不够,车辆轻量化的任何提升都无法弥补强度和质量的损失——胶粘和焊接也是如此。如果碎屑堵塞,会影响熔池,导致材料连接不良。连接不良会导致车辆对应力的响应较差,从而降低车辆的可靠性并容易出现缺陷。
访问零件
然后是触及范围的问题。专业人员在制造过程中能接触到零件吗?他们能从双面还是单面接触?即使你能从双面接触到零件,也会带来麻烦,增加时间和成本,使整个组装过程变得复杂。
目标位置的可达性限制在为特定应用选择*合适的制造技术时起着至关重要的作用。受限的空间会减少可用的技术选择,如果只有*种方法可行,则可能导致更高的成本和冗长的重新设计周期。在这种情况下,单面解决方案通过*大限度地提高可达性和设计灵活性,展现出显著的优势。
有些材料很难加工
假设你正在使用高强度和热压硬化钢。这些金属可能具有额外的耐久性和强度,但这种耐久性和强度也会带来*些后果。它们更耐切割和冲压。
因此,这些金属的韧性使其连接更具挑战性。虽然可以做到,但可能需要专门的工具和技术。这又会增加制造过程的时间和成本。
确保水密性和气密性
良好的密封件既防水又气密。这对于车辆性能和基本安全至关重要,尤其是在燃油系统和电气系统方面。如果金属连接不当,就会导致泄漏和腐蚀——这是任何制造商都不希望看到的。
缺乏连接或固定材料的知识
如果打造轻量化汽车就像更换材料*样简单就好了。但随着汽车材料的不断发展,工程师们有时会感到落伍。他们可能不了解连接轻量化合金和复合材料等新型*进材料的*新技术。
这并不是说工程师总是会落后于制造业的创新。但再次强调,缺乏对新材料的经验可能会在制造过程中浪费时间、金钱和精力。工程师可能需要花费培训时间来跟上进度。
连接强度的数学
振动、冲击、撞击,以及日常道路使用造成的磨损。驾驶员每天驾驶车辆时,这些动态力都会对车辆的连接件施加压力。如果连接件不够坚固,无法承受这些动态力,就会影响车辆性能,甚至可能危及车辆的基本安全。
这里的*个挑战是,工程师必须考虑连接所能承受的力。这不仅仅是计算*大力的问题,还包括连接在长期压力下如何保持耐久性。
连接异种材料
钢、铝和碳复合材料并非总是像花生酱和果冻*样容易混合。这些不同的材料具有不同的热性能、机械性能和物理性能。可靠的接头必须考虑到这些不同的性能,才能确保其强度足以满足轻量化车辆制造的需求。
铝加工起来很困难
铝有很多优点。它比其他金属更实惠,而且重量轻。然而,它有时成型和与其他金属连接起来可能比较困难。更高等*的铝,或形状复杂的铝部件,会给轻量化汽车制造带来各种变量。
由于铝材表面状态不*致,焊接前需要进行额外的处理,包括清洗和钝化。这些额外的步骤会延长生产时间,增加制造工艺的复杂性,并降低选择铝材所带来的预期成本节约。
面对所有这些挑战,有哪些方法可以提高轻型汽车制造的效率?
热力创新及其对轻量化汽车制造的影响
基于 SEF 等离子的解决方案可以解决甚至彻底解决许多此类问题。如果*项技术能够安全有效地粘合轻质材料,那么无需增加结构重量,就能打造出可靠耐用的产品。SEF 连接创新技术可以帮助克服上述诸多挑战。
但它也有助于具体了解这是如何实现的。让我们来看看*些热力创新,并探讨它们对轻量化汽车制造的影响:
等离子铆接技术 (TPR)将等离子技术与传统自冲铆接技术 (SPR) 相结合,突破了 SPR 的现有限制。这项创新技术能够以更低的力连接更高强度的超高强度钢 (UHSS) 顶层叠层,并使得使用 SPR 组装以前无法实现的材料组合成为可能。
因此,包括铝和混合材料在内的轻质金属板材无需预钻孔即可连接,目前抗拉强度高达 2,000MPa,厚度仅为 2 毫米。这不仅降低了设置力,无需冲压行程,还能降低噪音排放,使工艺更有利于设备与材料的结合,*终提高产品的耐用性和使用寿命。
等离子连接 (TPJ)是另*种基于等离子的连接技术,可提供单侧接入解决方案。该技术采用“等离子针”穿透金属板,确保卓越的结构性能。TPJ 利用等离子局部软化顶层金属板,无需预钻孔即可连接抗拉强度高达 2,000 MPa 的钢材。即使连接异种材料,该方法也能形成牢固可靠的连接,从而提升了工艺的多功能性和有效性。
螺柱焊接系统也使用等离子,但主要用于螺柱焊接前金属表面的预处理。螺柱焊接头上安装的等离子清洁装置在螺柱焊接前运行,以确保理想的清洁表面。这样每次都能提供相同的清洁状态,从而保证稳定的螺柱焊接工艺,并提升接头质量。
自动清洁 (TAC)是*款用于金属板表面的清洁系统。它可以为焊接、TIG 焊接或胶接等工序做好表面准备。由于表面没有油污或其他污染物,飞溅更少,因此可以减少焊后清洁工作。有趣的是,焊枪安装在*个可以进行线性清洁的机器人上。这种方法*终可以作为*个“独立”的解决方案。
这些创新如何影响轻量化汽车制造?在采用轻量化合金和铝材时,确保牢固耐用的接合和接头对于满足制造和长期消费者使用的需求至关重要。虽然减轻车重仍然是*个关键目标,但实现这*目标需要采取综合方法,优*考虑材料完整性和结构可靠性。
有了上述热技术创新,许多难题得以避免。TPJ 和 TPR 等解决方案能够连接此前不兼容的材料,拓展了下*代汽车的设计可能性。例如,您可以提高材料兼容性,或提升处理混合金属的能力。但它们的优势远不止于此。不妨考虑以下优势:
优化表面处理:妥善处理金属表面可增强其对焊接、TIG 焊接或粘合剂等连接工艺的适应性。由于这些工艺需要清洁的表面才能获得*佳性能,因此更**、更全面的清洁工艺将直接惠及轻量化汽车制造。
提升连接效率: SPR 技术应用范围的扩展,为整车增添了新的应用能力,突破了通常需要专用铆钉和模具才能实现的标准限制。例如,TPR 和 TPJ 在连接铝铸件等部件时均具有显著优势。这些工艺中涉及的热传递有利于铝的变形,且不会产生裂纹,因此对于 F 状态铝铸件尤其有效,而 F 状态铝铸件在白车身 (BIW) 设计中越来越普遍。
经济**的制造:无需预钻孔,并拥有更丰富的技术选择,使轻量化车辆生产更具经济可行性。此外,更佳的焊接质量和更少的飞溅,*大程度地减少了昂贵的二次清理需求,进*步降低成本并提**率。
良好的热技术创新不仅能使轻量化汽车制造更坚固,而且在商业层面也更具实用性。连接工艺越**,制造成本就越低廉。
将热技术创新引入轻型汽车制造
新技术正在改变轻量化汽车制造,而这并非总是源于新材料的引入。史丹利工程紧固件公司 (STANLEY Engineered Fastenings) 的热力创新技术,可提高清洁度和连接性能,使两块轻质金属板更容易连接在*起,从而为您提供更多轻量化制造选择,且无需额外成本。这意味着您可以生产安全、可靠、优质的汽车零部件,从而减少发动机的碳排放。